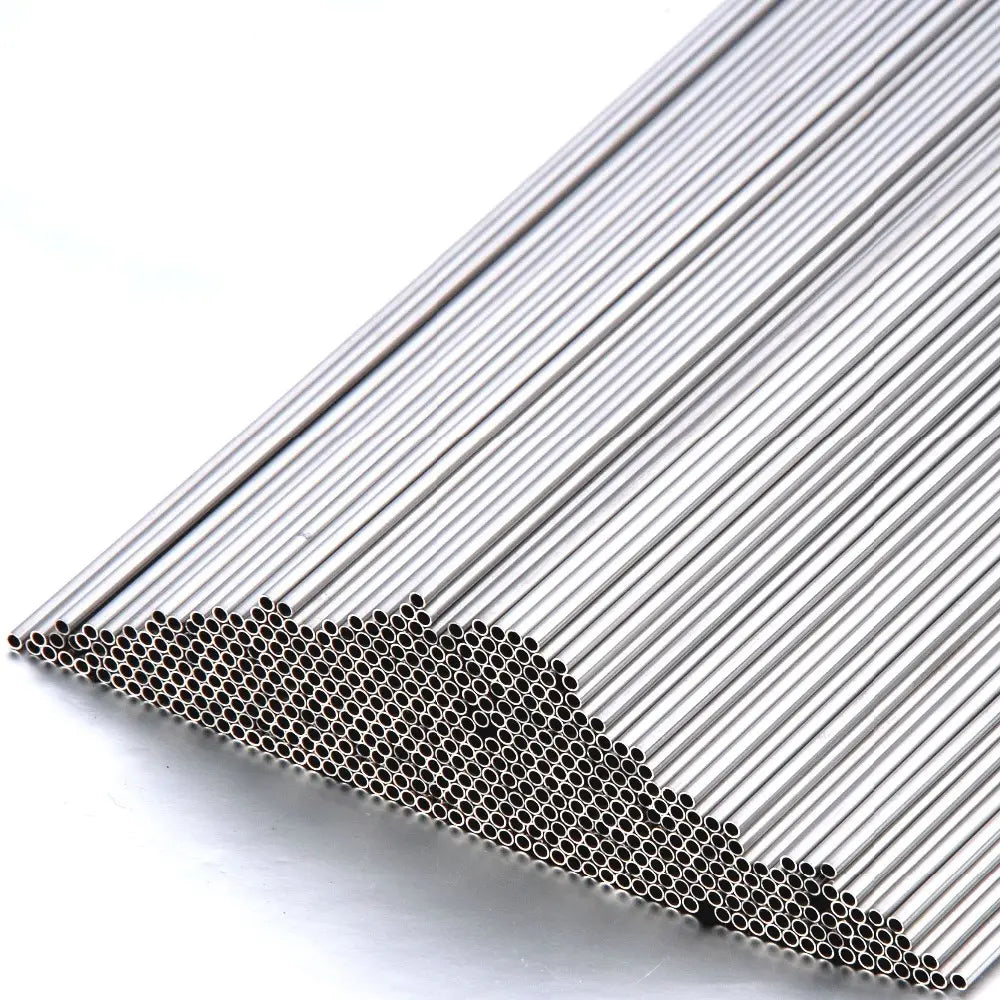
Is stainless steel stronger than rebar?
Table of Contents
1. Introduction
Brief overview of stainless steel and rebar as construction materials:
Stainless steel and rebar are two fundamental materials in modern construction, each serving distinct purposes. Stainless steel is an iron-based alloy containing a minimum of 10.5% chromium, which provides exceptional corrosion resistance through the formation of a protective oxide layer. It comes in various grades, each designed for specific applications. Rebar, short for reinforcing bar, is typically made from carbon steel and is designed specifically to reinforce concrete structures. Its primary role is to provide tensile strength to concrete, which is naturally strong in compression but weak in tension.
The importance of understanding material strength for engineering and construction:
Understanding material strength is crucial in construction and engineering for several critical reasons. First, it directly affects the safety and stability of structures, ensuring they can withstand expected loads and environmental stresses. Second, proper material strength knowledge enables engineers to optimize design efficiency, preventing both over-engineering (which wastes resources) and under-engineering (which compromises safety). Additionally, material strength considerations impact project costs, maintenance requirements, and overall structure longevity. Engineers must balance these factors to create safe, efficient, and economical designs that meet building codes and project specifications.
Comparing the strength and properties of stainless steel versus rebar:
The primary objective of this comparison is to provide a clear understanding of how stainless steel and rebar differ in terms of their mechanical properties and performance characteristics. This comparison will examine several key aspects: tensile strength, yield strength, durability, and corrosion resistance.By analyzing these properties, we can better understand which material is more suitable for specific applications and environmental conditions. This knowledge is essential for making informed decisions in construction projects, particularly when dealing with challenging environments or specialized structural requirements. The comparison will also consider cost implications and long-term performance to provide a comprehensive understanding of both materials.
2. Strength and Mechanical Properties
Tensile strength: Comparing stainless steel and traditional carbon steel rebar:
When examining tensile strength, we find notable differences between stainless steel and traditional carbon steel rebar. Stainless steel typically exhibits tensile strength ranging from 515 to 827 MPa (megapascals), with austenitic grades like 316L reaching up to 620 MPa and duplex grades achieving even higher values. In comparison, traditional carbon steel rebar generally offers tensile strength between 480 to 620 MPa. What's particularly interesting is that while both materials can achieve similar base tensile strengths, stainless steel maintains its strength properties even under extreme temperature conditions and corrosive environments, whereas traditional rebar may experience strength degradation under these conditions.
Yield strength and ductility: Which material is better suited for structural applications?
The yield strength and ductility characteristics of these materials play crucial roles in structural applications. Stainless steel typically demonstrates yield strength between 205 to 410 MPa, coupled with excellent ductility that allows for significant deformation before failure. This combination makes it particularly valuable in seismic zones and structures requiring high plastic deformation capacity. Traditional carbon steel rebar, with yield strengths ranging from 250 to 350 MPa, also provides good ductility but may show less elongation before failure. The higher ductility of stainless steel can be advantageous in structures that need to absorb energy and resist sudden loads, though both materials meet building code requirements for structural applications when properly specified.
Discussion on how alloy composition affects strength:
The composition of these materials significantly influences their strength properties. In stainless steel, the primary strength-enhancing elements include:
-
Chromium (minimum 10.5%): Besides providing corrosion resistance, it contributes to strength through solid solution strengthening
-
Nickel: Enhances strength while improving ductility and toughness
-
Molybdenum: Increases strength and improves pitting corrosion resistance
-
Nitrogen: Significantly improves strength, particularly in austenitic grades
For traditional carbon steel rebar, strength primarily comes from:
-
Carbon content (typically 0.18-0.4%): The primary strength-providing element
-
Manganese: Improves hardenability and strength
-
Heat treatment processes: Crucial for developing desired strength properties
The interaction between these elements creates distinct microstructures that determine the final mechanical properties. For instance, duplex stainless steels achieve their high strength through a balanced microstructure of austenite and ferrite phases, while carbon steel rebar relies more heavily on heat treatment and carbon content for strength development.
This complex interplay of alloying elements and processing methods helps explain why different grades of both materials can achieve varying strength levels, allowing engineers to select the most appropriate option for specific applications based on both strength requirements and environmental conditions.
3. Corrosion Resistance
Highlighting stainless steel's superior corrosion resistance, especially in harsh environments:
Stainless steel's exceptional corrosion resistance stems from its unique chemical composition, particularly its chromium content of at least 10.5%. This chromium forms a self-healing passive oxide layer on the surface, providing continuous protection against corrosive elements. In harsh environments, stainless steel demonstrates remarkable durability through:
-
Resistance to atmospheric corrosion, even in industrial and marine environments
-
Ability to withstand chemical exposure, including acids and alkaline solutions
-
Protection against pitting and crevice corrosion, especially in grades containing molybdenum
-
Maintenance of structural integrity even at elevated temperatures
-
Prevention of stress corrosion cracking through specialized grade selection
Limitations of traditional rebar in corrosive conditions:
Traditional carbon steel rebar faces significant challenges in corrosive environments:
-
Rapid deterioration when exposed to chlorides, particularly in marine environments
-
Vulnerability to moisture penetration through concrete, leading to oxidation
-
Expansion due to rust formation, causing concrete cracking and spalling
-
Reduced service life in structures exposed to de-icing salts
-
Progressive weakening in underground structures exposed to aggressive soils
-
Accelerated corrosion in industrial environments with high pollution levels
The corrosion process creates iron oxide (rust), which occupies up to six times the volume of the original steel, leading to concrete damage and structural integrity issues.
Examples of when stainless steel rebar is preferred over carbon steel rebar:
Stainless steel rebar becomes the preferred choice in several specific applications:
-
Coastal and Marine Structures:
-
Bridge decks and piers in saltwater environments
-
Seawalls and harbor facilities
-
Coastal residential and commercial buildings
-
Offshore platforms and marine terminals
-
Transportation Infrastructure:
-
Bridge expansion joints and deck portions exposed to de-icing salts
-
Highway sound barriers in northern regions
-
Tunnel linings in maritime areas
-
Airport pavements exposed to de-icing chemicals
-
Industrial Applications:
-
Chemical processing plant foundations
-
Water treatment facilities
-
Power plant structures
-
Mining facility infrastructure
-
Critical Infrastructure:
-
Nuclear power plant containment structures
-
Historic preservation projects requiring long-term durability
-
Medical facilities with strict structural integrity requirements
-
Data center foundations in coastal areas
-
Environmental Exposure:
-
Structures in areas with high humidity and temperature fluctuations
-
Buildings in industrial zones with corrosive atmospheric conditions
-
Underground structures in aggressive soils
-
Waterfront developments with direct exposure to seawater spray
In these applications, the higher initial cost of stainless steel rebar is justified by:
-
Extended service life (often 75-100 years versus 25-50 years for traditional rebar)
-
Reduced maintenance requirements
-
Lower lifecycle costs
-
Enhanced structural reliability
-
Minimized repair and replacement needs
This superior corrosion resistance makes stainless steel rebar particularly valuable in projects where long-term durability is crucial and replacement or repair would be difficult or costly.
4. Cost-Effectiveness and Application
Initial cost versus long-term benefits: Durability of stainless steel vs. affordability of rebar:
The cost comparison between stainless steel and traditional rebar presents a complex economic analysis:
Initial Costs:
-
Stainless steel: $4.50-7.00 per pound
-
Traditional rebar: $0.50-0.80 per pound
-
Initial cost ratio: Stainless steel is typically 6-8 times more expensive
Long-term Benefits of Stainless Steel:
-
Extended service life (75-100 years vs 25-50 years for traditional rebar)
-
Minimal maintenance requirements
-
Reduced repair and replacement costs
-
Lower inspection frequency needs
-
Decreased risk of structural failure
Life Cycle Cost Analysis:
-
Traditional rebar may require multiple repairs/replacements over structure lifetime
-
Maintenance costs for traditional rebar can exceed initial savings within 20-30 years
-
Labor costs for repairs are often higher than material costs
-
Business disruption during repairs adds hidden costs
Specific use cases where stainless steel or standard rebar is more practical:
Stainless Steel Best Applications:
-
Coastal Construction:
-
Marine facilities
-
Oceanfront buildings
-
Harbor infrastructure
-
Critical Infrastructure:
-
Nuclear facilities
-
Chemical plants
-
Healthcare facilities
-
Water treatment plants
-
High-Risk Environments:
-
Areas with heavy de-icing salt use
-
Underground structures in aggressive soils
-
Industrial zones with corrosive atmospheres
Standard Rebar Best Applications:
-
Residential Construction:
-
Home foundations
-
Driveways
-
Interior structural elements
-
Commercial Buildings:
-
Office buildings in non-coastal areas
-
Parking structures in mild climates
-
Retail facilities in standard environments
-
Basic Infrastructure:
-
Interior highway sections
-
Urban buildings in non-aggressive environments
-
Temporary structures
The role of material strength in determining cost efficiency:
Material Strength Considerations:
-
Design Optimization:
-
Higher strength can allow for reduced material usage
-
Smaller cross-sections may be possible with stronger materials
-
Labor costs may decrease with less material handling
-
Safety Factors:
-
Higher strength materials often allow lower safety factors
-
Reduced material volume requirements
-
More efficient structural designs
-
Economic Impact:
-
Material strength affects overall structure size
-
Foundation requirements may vary with material choice
-
Transportation and installation costs correlate with material volume
Cost Efficiency Factors:
-
Load Requirements:
-
Higher loads justify stronger materials
-
Critical structural elements may warrant premium materials
-
Non-critical elements can use standard materials
-
Environmental Exposure:
-
Harsh environments justify higher material costs
-
Protected locations can use standard materials
-
Exposure levels influence maintenance costs
-
Project Lifecycle:
-
Long-term projects benefit from premium materials
-
Temporary structures can use standard materials
-
Replacement accessibility affects material choice
This comprehensive analysis helps engineers and project managers make informed decisions based on both immediate costs and long-term value, ensuring the most cost-effective solution for each specific application.
5. Conclusion
Summary of key points: When strength, corrosion resistance, and cost matter most:
The comparative analysis of stainless steel and traditional rebar reveals distinct scenarios where each material excels:
Strength Considerations:
-
Stainless steel offers slightly higher tensile strength (515-827 MPa)
-
Traditional rebar provides adequate strength (480-620 MPa) for most applications
-
Both materials meet standard building code requirements
Corrosion Resistance:
-
Critical in coastal environments
-
Essential for structures exposed to de-icing salts
-
Vital for chemical and industrial facilities
-
Determines long-term structural integrity
Cost Implications:
-
Initial investment vs. lifecycle costs
-
Maintenance and replacement expenses
-
Project duration and accessibility
-
Environmental exposure severity
Final verdict: Is stainless steel stronger than rebar, and does it justify its application?
While stainless steel can exhibit marginally higher strength values, the strength difference alone rarely justifies its selection over traditional rebar. The true value proposition of stainless steel lies in its combination of:
-
Comparable strength properties
-
Superior corrosion resistance
-
Extended service life
-
Reduced maintenance requirements
-
Enhanced long-term reliability
The selection between stainless steel and traditional rebar should be based on:
-
Project-specific requirements
-
Environmental conditions
-
Design life expectations
-
Maintenance accessibility
-
Budget constraints
Encouragement for engineers and builders to evaluate material choices based on project needs:
Engineers and builders should consider:
-
Project Assessment:
-
Carefully evaluate environmental exposure conditions
-
Consider the structure's intended service life
-
Assess maintenance accessibility and costs
-
Calculate total lifecycle costs
-
Risk Analysis:
-
Evaluate consequences of potential failure
-
Consider public safety implications
-
Assess environmental impact
-
Review regulatory requirements
-
Future Considerations:
-
Plan for potential changes in environmental conditions
-
Consider future maintenance capabilities
-
Account for evolving building codes
-
Factor in potential retrofitting needs
The key to successful material selection lies in balancing:
-
Technical requirements
-
Environmental conditions
-
Economic constraints
-
Long-term performance needs
By carefully considering these factors, professionals can make informed decisions that optimize both performance and cost-effectiveness for their specific applications, ensuring sustainable and reliable construction solutions for the future.