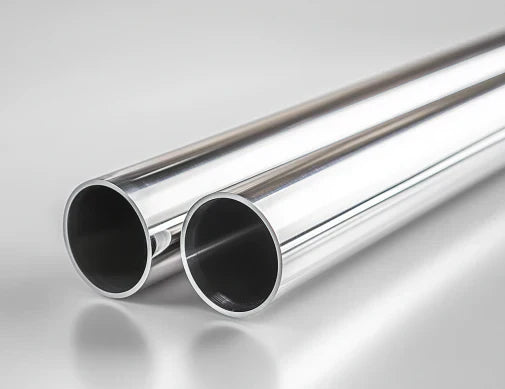
can you weld stainless steel with a regular mig welder
Table of Contents
- Introduction & Summary
- What Is MIG Welding?
- Can You Use a Regular MIG Welder?
- Picking the Right Wire
- Gas Matters
- Setting Up Your Machine
- Cleaning the Metal
- How to Test Stainless Steel
- Do You Need a Special Welder?
- Common Mistakes to Avoid
- What Can You Make or Fix?
- How Does the Weld Look?
- Testing the Weld
- Conclusion
Introduction & Summary
When people ask, “Can you weld stainless steel with a regular MIG welder?”, the answer is yes — you definitely can! But like most things in life, it’s not just a simple “yes” or “no.” There are a few things you need to know to do it the right way and avoid problems later on. If you’ve got a MIG welder at home or in your shop, and you’re thinking about trying it on stainless steel, this blog is for you.
What Is MIG Welding?
Let’s keep it super simple: MIG welding (Metal Inert Gas welding) is when you use a machine that feeds wire and gas to melt and join metal together. It’s like a hot glue gun but for metal. The wire melts, the gas keeps the air away, and the metal pieces stick together as they cool.
A regular MIG welder is usually set up for mild steel or basic metal jobs. But stainless steel? That’s a whole different beast.
Can You Use a Regular MIG Welder?
Yes, you can — but you’ll need a few adjustments. Stainless steel isn’t impossible to weld, but it does behave differently from regular steel. The goal is to make a strong weld that doesn’t rust, warp, or look terrible.
Here’s what you’ll need to think about:
- The right wire for stainless steel
- The correct shielding gas
- Adjusting your welder settings
- Good cleaning and prep
Let’s break each one down in plain English.
Picking the Right Wire
You can’t use the same wire you use for regular steel. That stuff won’t work on stainless and may cause the weld to rust or fall apart. You need stainless steel MIG wire — and there are different types depending on what kind of stainless you’re welding.
The most common wire for general jobs is ER308L. It works well for stainless steel 304 vs 18/8, which are basically the same thing in most home or shop welding scenarios. Both 304 and 18/8 stainless are high-quality, corrosion-resistant types often used in kitchen items, sinks, and construction. So if you're fixing a stainless steel beam or fabricating something with 304 or 18/8, this wire is your go-to.
Gas Matters
The gas you use during MIG welding keeps the weld clean and strong. For regular steel, people usually use a mix of argon and carbon dioxide. That won’t work for stainless steel — it makes the welds look messy and increases the chance of rust.
Instead, use a mix like 98% argon and 2% CO₂, or a tri-mix with argon, helium, and CO₂ if you want top-quality results. Your weld will look better and last longer. If you're serious about doing it right, this is one step you can’t skip.
Setting Up Your Machine
Here’s where things can get tricky if you’ve never welded stainless before. Stainless steel is more sensitive to heat. If you overheat it, you’ll warp it or discolor it — those ugly rainbow colors mean trouble.
To avoid that:
- Keep your amperage (heat) just right — not too hot
- Watch your wire speed
- Practice on scrap stainless before going to your final piece
Welding something like a stainless steel beam means you're working with thicker material, so you’ll need more heat — but still within limits. Keep the welds short and let them cool to prevent warping.
Cleaning the Metal
No matter what you're welding, clean surfaces are a must. But for stainless steel, this is non-negotiable.
Before you weld:
- Clean the metal with acetone or alcohol
- Use a stainless wire brush (don’t mix it with carbon steel)
- Remove any rust, paint, or dirt
Want to test if something is stainless steel before you start? Try this: use a magnet. Stainless steel like 304 or 18/8 is usually not magnetic (or only weakly). If the magnet sticks strong, it might not be real stainless. Another way is to grind a bit — stainless gives off fewer, shorter sparks compared to regular steel.
Knowing how to test if something is stainless steel helps you avoid welding the wrong type and ending up with weak or rusty welds.
How to Test Stainless Steel
To test if a metal is stainless steel, start with a magnet—most stainless steels like 304 are only weakly magnetic or not at all. Next, check for rust resistance by exposing the surface to moisture; stainless should resist rusting. You can also grind the surface—stainless steel produces short, bright sparks. For accurate results, use a chemical test kit or a metal analyzer to confirm the grade. Knowing how to test stainless steel helps avoid mistakes in welding or fabrication.
Do You Need a Special Welder?
Nope! Your regular MIG welder can handle it with the right wire and gas. Of course, if you’re doing high-end or heavy industrial work, a specialized machine might be better. But for home repairs, DIY projects, and small business needs, a basic MIG welder will get the job done just fine.
Common Mistakes to Avoid
Let’s go over a few things you don’t want to do:
- Using the wrong wire – Regular steel wire won’t cut it.
- Wrong gas – CO₂ or air exposure ruins the weld.
- Overheating the metal – Keep it cool to avoid distortion.
- Dirty surfaces – Any contamination weakens the weld.
- Wrong stainless type – Know your material before welding.
If you’re working with stainless steel 304 vs 18/8, remember: they’re very similar, so the same wire and gas will usually work for both. But if you’re unsure what kind of stainless you’re welding, test it first.
What Can You Make or Fix?
There’s a lot you can do once you master MIG welding on stainless:
- Kitchen counters and splashbacks
- Handrails and frames
- Exhaust systems
- Custom furniture
- Stainless steel beams and brackets for small structures
Just remember to seal or coat your welds if they’ll be exposed to moisture, especially outdoors.
How Does the Weld Look?
Stainless steel welds can look really clean — almost shiny — if you do it right. But they can also look dull and discolored if the gas coverage wasn’t good or if the metal got too hot. Don’t worry if your first try isn’t perfect. Clean up the welds with a stainless brush or a flap disc, and polish them up if needed.
Testing the Weld
Once your weld is done and cleaned, it should be:
- Smooth and free of holes or gaps
- Even in width and shape
- Strong – give it a tap test or even try to bend the joined pieces (carefully!)
If you're not sure your piece is really stainless, remember: knowing how to test if something is stainless steel before welding avoids wasting time and materials.
Conclusion
If you’ve got a regular MIG welder, don’t be afraid to try welding stainless. With the right wire, gas, clean surface, and patience, you can make solid, rust-free welds on stainless items, even big jobs like stainless steel beams.
Just remember:
- Use stainless MIG wire (ER308L works well for stainless steel 304 vs 18/8)
- Get the correct shielding gas
- Clean your materials before you start
- Take your time and practice
Once you get the hang of it, welding stainless steel with a MIG welder becomes just another handy skill in your DIY toolbox. So fire up that machine, test your metal, and start welding!