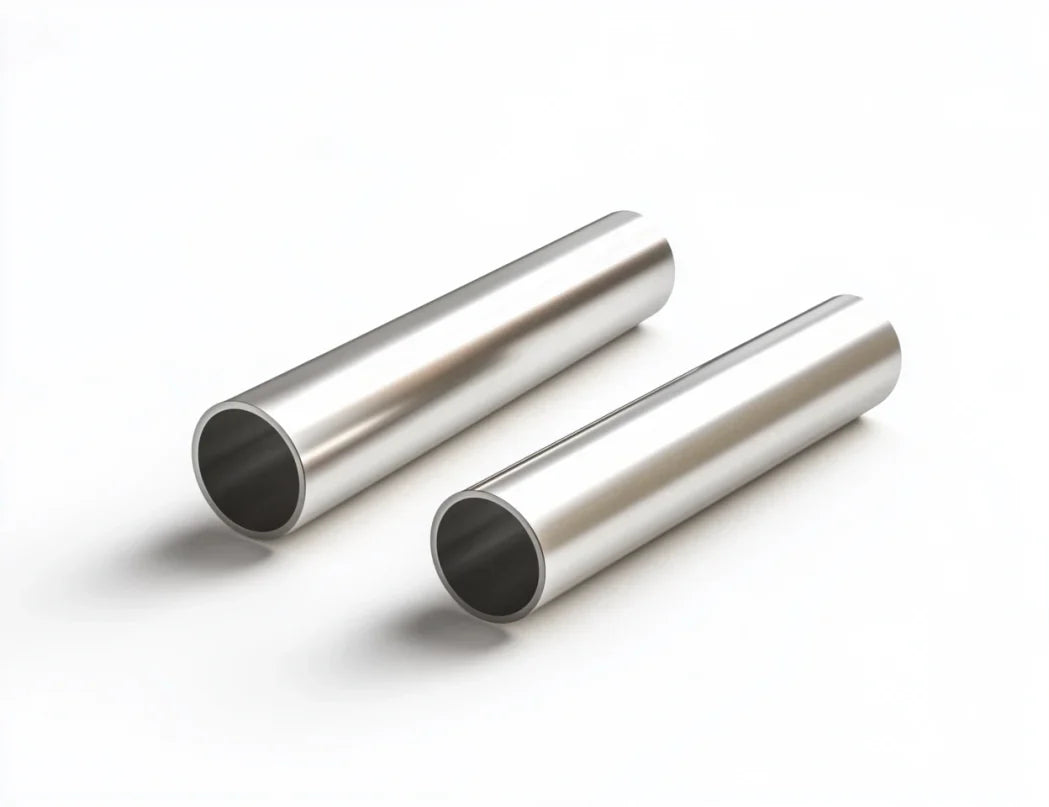
How to Weld Stainless Steel Pipe
Table of Contents
- Introduction
- What Makes Stainless Steel Pipes Tricky to Weld?
- Tools and Materials You’ll Need
- Step-by-Step: How to Weld Stainless Steel Pipe
- Common Problems and How to Fix Them
- What If You’re Working with Different Shapes?
- Tips for Getting Better at Welding
- Where You Might Use Welded Stainless Steel Pipes
- Final Thoughts
Introduction
If you've ever wondered how to weld stainless steel pipe, you're not alone. Stainless steel looks great, lasts a long time, and doesn’t rust easily, so it’s used everywhere—from kitchen sinks to big factories. But when it comes to welding it, many people get nervous. They think it’s too hard or that you need to be a professional. The good news? With a little guidance, patience, and practice, anyone can learn how to do it the right way.
In this blog, we’ll break everything down in plain English—no confusing words, no fancy talk. Just easy-to-follow tips and steps to help you get started. Whether you're trying to fix a broken pipe, build a custom frame, or connect some square stainless steel tubing, you’re in the right place.
What Makes Stainless Steel Pipes Tricky to Weld?
Let’s start by understanding why stainless steel needs extra attention when welding.
Stainless steel is great because it resists rust and corrosion. That’s why it’s used in places with water or chemicals—like kitchens, bathrooms, and even hospitals. But because it doesn’t handle heat the same way regular steel does, you have to be careful. If it gets too hot, it can lose its shiny look, weaken the metal, or even make it rust over time. And trust us, nobody wants a rusty pipe that’s supposed to be rust-proof.
So the key is to control the heat and keep everything clean.
Tools and Materials You’ll Need
Before you start welding, gather what you need. Here’s a simple list:
- A stainless steel pipe (of course!)
- Welding machine (any standard one can do, especially for home use)
- Safety gear (gloves, eye protection, and a good welding helmet)
- Cleaning tools (like a wire brush or sandpaper)
- Clamps to hold the pipe steady
- Filler rods or wire (these help join the pipes)
If you're working with additional parts like stainless steel strips or stainless steel perforated sheets, keep them handy too. These might be used for supports, covers, or connections depending on what you’re building.
Step-by-Step: How to Weld Stainless Steel Pipe
Let’s walk through the process one step at a time.
1. Clean Everything First
This might sound boring, but it’s really important. Stainless steel hates dirt and grease when being welded. Use a clean rag and some alcohol to wipe down the pipes. Then go over the edges with a wire brush or sandpaper. Even if the pipe looks shiny, tiny bits of oil or rust can mess up your weld.
Also, make sure your stainless steel strips or other pieces are clean too.
2. Secure the Pipe
Use clamps to hold the pipe in place. If the pipe moves while you're welding, the connection will be weak or crooked. If you're welding two pipes together, line them up carefully. It helps to mark the spot with a marker so you know where to weld.
If you’re attaching the pipe to a sheet, like stainless steel perforated sheets, be sure it sits flush—no gaps or bumps.
3. Test Your Settings
Before you go all-in, it’s smart to do a small test on a scrap piece of stainless steel. Every welding machine is a little different. This helps you get the heat and speed just right. You want the metal to melt just enough to join, but not so much that it turns dull or blue.
4. Start Welding Slowly
Now for the fun part! Start at one end of the pipe and move slowly across the joint. Keep your hand steady and your eyes on the puddle of melted metal. The trick is to move at the same pace the whole time.
Don’t rush it—going too fast can leave holes. Going too slow can make it too hot and damage the steel. You’ll get better with practice.
5. Let It Cool Naturally
Once you’re done, let the metal cool on its own. Don’t splash it with water. Fast cooling can make the steel crack or warp. Give it a few minutes, and then check your work.
6. Clean the Weld
Welding often leaves some burn marks or little bumps. Use your wire brush again to clean up the area. If you want a polished look, you can sand it down and even buff it with a polishing wheel. This also helps keep the pipe strong and prevents rust from forming at the weld spot.
Common Problems and How to Fix Them
Here are a few issues people often face—and simple ways to avoid them.
Problem 1: The Weld Looks Dirty
This usually happens if the metal wasn’t clean or the machine settings were off. Always clean your pipes, and double-check the heat setting before starting.
Problem 2: The Pipe Warps
Too much heat can bend your pipe out of shape. Use smaller bursts of weld instead of doing it all at once. Let it cool between passes if needed.
Problem 3: The Pipe Rusts After Welding
This is a big one. Welding can sometimes remove the rust-proof layer from stainless steel. If this happens, use a polish or a special stainless steel cleaner to restore the surface. Also, try not to use tools that have touched regular steel before—they can transfer particles that cause rust.
What If You’re Working with Different Shapes?
Sometimes, you’re not just welding round pipes. Maybe you’re connecting to square stainless steel tubing or adding a cover made from stainless steel perforated sheets.
The steps are mostly the same:
- Clean the surface
- Clamp everything tightly
- Test your heat
- Weld carefully
- Clean and cool
Just be sure the joints are smooth and the pieces fit tightly together before you weld. Square tubing might take a bit more time to line up, but once it’s clamped, it’s just as easy to work with.
Tips for Getting Better at Welding
If you’re new to welding, don’t worry. Here are some friendly tips to help you improve:
- Practice on scrap metal first. You don’t want to mess up your good pipes right away.
- Watch videos online. Sometimes seeing someone else do it makes it easier to understand.
- Don’t weld when you're tired. It takes focus and a steady hand.
- Start with small projects. Fix a broken frame or build a simple holder before jumping into big pipe systems.
- Ask questions. Welding forums and local hardware stores often have helpful folks ready to share tips.
Where You Might Use Welded Stainless Steel Pipes
Once you get good at welding, the possibilities are endless. Here are a few practical uses:
- Repairing broken pipes in the kitchen or bathroom
- Building frames for outdoor furniture
- Connecting stainless steel strips for a custom shelf or rack
- Creating railing systems with square stainless steel tubing
- Building covers or guards using stainless steel perforated sheets
You can even start your own small welding projects as a side hustle or home improvement hobby.
Final Thoughts
Welding stainless steel pipe doesn’t have to be scary. With the right tools, a clean workspace, and a bit of patience, you can do it yourself. Just remember the basics: keep it clean, control the heat, and take your time. And don’t forget—practice makes perfect.
Whether you’re fixing up a leak, building a new frame, or working with stainless steel strips, square stainless steel tubing, or stainless steel perforated sheets, these steps will help you get a strong, clean weld that lasts.
So grab your gloves, power up your machine, and give it a go. Stainless steel might be tough, but with these tips, so are you.